Resources
MicroSeal™ Product Selection Guide
The MicroSeal TM family is a complete line of high purity, high integrity seals for industrial and semiconductor applications including low flow, high flow, high pressure and low pressure drop. We also offer orifice seals and blind seals to cap off spare ports. Other key benefits include high cleanliness and passive, chrome rich, low Ra surface finishes. MicroSeals retrofit to standard “C” seal systems. Our seals meet SEMI Standard PR 3.1, 3.5 and new high-flow standards.
The MicroSeal design has a softer, more compliant interface that molds itself to the mating surface ensuring leak tightness, and eliminating virtual leaks without sacrificing rebound characteristics. This is the only high compliance seal on the market with high rebound.
MicroSeals rebound rate exceeds competing seal designs by as much as ten times and they are particularly forgiving of cavity tolerance. This ensures that the sealing surfaces stay in intimate contact during pressure, temperature and vibration extremes. All these characteristics are achieved with low compression rates, ensuring high first pass yield.
Key MicroSeal Benefits
✓ Lowest Pressure Drop Design
✓ Optimized I.D. Bore for Lowest Pressure Drop In Medium Flow, High Flow, Vapor and
Liquid Delivery Systems
✓ Lowest Compression to Ensure Highest Reliability of Gas / Liquid Delivery Systems
✓ 10x’s Seal Rebound vs. Traditional designs to achieve Leak Integrity under Shock and
Vibration (Patented)
✓ SEMI PR 3.1 and 3.5 Compliant
✓ Ultra High Purity Double Melt 316 Stainless Steel
✓ Ultraclean Passive Chrome Rich Surface
✓ 5 Ra wetted surface finish
✓ Compressor Ring Design Eliminates Virtual Leaks (Patented)
✓ Exceptional First Pass Yield on Seal Makeup - Virtually Eliminates High Cost Rework an
Scrap
✓ Rapid Delivery
MICROSEALTM MODULAR SURFACE MOUNT SEAL TEST SUMMARY
PERFORMANCE TEST | ACCEPTANCE CRITERIA | PERFORMANCE |
Material |
316L VIM VAR |
>0.004% Sulfur content |
Leak Tests, Design Pressure (5000 psig) |
Outboard leakage: <1 x 10⁻⁹ atm·cc/sec He |
Outboard leakage: <7 x 10⁻¹¹ atm·cc/sec He at 100 psig after exposure to 5000 psig |
Pressure Tests-Proof at 7500psig Burst Test (hydrostatic) |
No hydrostatic test fluid shall be visible. Inboard leakage: <7 x 10⁻¹¹ atm·cc/sec He |
No hydrostatic test fluid visible. |
Vibration-MILSPEC 810E Sec 1 Category 1 Shock – Drop test in 25G increments |
Inboard leakage: <1 x 10⁻⁹ atm·cc/sec He after testing No Spec on Shock |
Inboard leakage: <7 x 10⁻¹¹ atm·cc/sec He after MIL-SPEC 810E Sec 1-3 category 1test. Shock exceeding >294G’s – No leaks |
Pre-load Safety Factor | Inboard leakage: <1 x 10⁻⁹ atm·cc/sec He at 80% and 120% of manufacturers’ specified torque setting. |
Inboard leakage: <7 x 10⁻¹¹ atm·cc/sec He at 10, 15, 24, 30, 36, and 48 in/lbs torque. |
Repeatability-Make and remake substrate with 20 sets of new seals. |
Inboard leakage: <1 x 10⁻⁹ atm·cc/sec He after 20 re-make cycles. |
Passed Inboard leak: <7 x 10⁻¹¹ atm·cc/sec He at each make and remake and after 20 re-make cycles. Tested at 10, 24, and 48 in/lbs torque |
Torsion | Inboard leakage: <1 x 10⁻⁹ atm·cc/sec He after testing at 50,75,and 100 ft/lbs. |
Inboard leakage: <5 x 10⁻¹¹ atm·cc/sec He after torque test. |
Temperature Cycling | Inboard leakage: <1 x 10⁻⁹ atm·cc/sec He after temperature testing. Three sets of two port seals room temperature, 100°C, room temperature, -10°C; five cycles |
Inboard leakage: Passed leak test <7 x 10⁻¹¹ atm·cc/sec He at each temperature. |
Temperature Shock Test | Shock 200°C to -196°C | Shock test +200°C to -196°C (direct insertion into Liquid N2) No Leaks at <7 x10⁻¹¹ atm·cc/sec He |
Compression Load Test | Compress from .062 to .050 inch Measure Load |
Standard Seal - 685 lbs Low Load Seal - 618 lbs |
Photos of counterbore characteristics
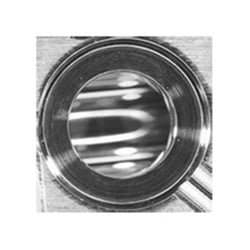
Good
Burnished
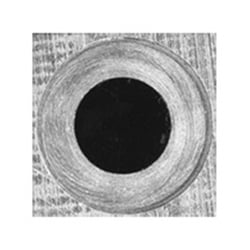
Reject
Non-Concentric - Tool Marks
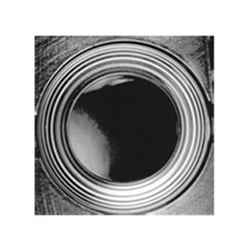
Reject
Damaged - Burnished tool
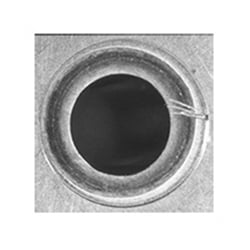
Reject
Scratch
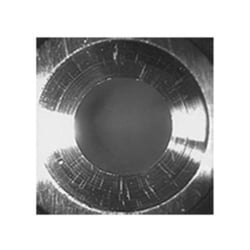
Reject
Chatter
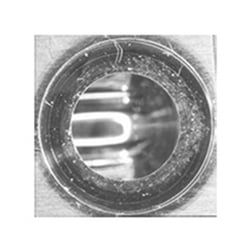
Reject
Dirt